Very High Cycle Fatigue Testing (VHCF)
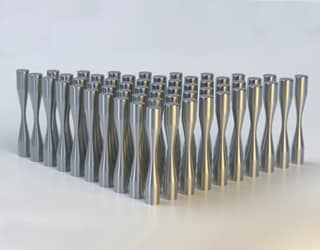
1010 Cycles in 6 Days
Rapid prototyping using additive manufacturing techniques has increased the need for faster methods to characterize the fatigue behavior of 3D-printed alloys. Fatigue testing instruments utilizing ultra-sonic (20kHz) sample resonance enable testing to 107 cycles in about 10 minutes versus over 10 hours using standard instrument designs. Ultra-sonic fatigue measurements also allow sample testing to extremely high cycles (1010) in a reasonable timeframe allowing insight to material failure behavior beyond the traditional “fatigue limit” of 107 cycles.
Featured Applications
Ultrasonic Fatigue Testing for Additively Manufactured Metal Alloys
Compared with traditional fatigue testing, the ultrasonic method achieves much speedier results along with the ability to run extremely high test cycles in a reasonable time frame.
Used with permission. ©ASM International.
Effects of Defects in Very High Cycle Fatigue of Additively Manufactured AlSi12
This article explores the relationship between the production process, the structure, and the properties of AlSi12 alloy in detail. The research was undertaken to determine the effect of process variables on the microstructure features. Mechanical properties ranging from hardness and quasi-static behavior to very high cycle fatigue (VHCF) behavior have been investigated. The damage processes in HCF and VHCF areas using the morphology of internal defects and microstructural features were analyzed. The findings may be utilized to develop a cumulative approach for controlling the SLM process parameters required for the desired microstructure and for calculating residual porosity to properly predict mechanical behavior under fatigue loading.
Detection of Inclusions in Metal Materials Using an Ultrasonic Fatigue Testing System
The ultrasonic fatigue testing system used for this experiment enables testing at a frequency of 20 kHz, achieving a test with 109 cycles in about 14 hours. Such a system is very effective to detect internal inclusions through actual fatigue testing. In this experiment, we performed the detection of inclusions in an SNCM439 specimen using the ultrasonic fatigue testing system, USF-2000A, and observed the inclusions using the electron probe micro analyzer, EPMA, to identify their elements.
Observation of Bending Fatigue Testing of Metal Plate at Ultrasonic Frequency
Fatigue testing of a target component conducted using the ultrasonic frequency was documented using the HPV-X2, and the movement characteristics of the test specimens were confirmed. The HPV-X2 proved to be effective in capturing the high-speed movement generated during the test, and installation of a microscope permitted visual documentation of these minute movements. Aside from this confirmation of movement in the specimen during the test, the actual degree of movement in the test specimen can be determined from the captured images. The USF-2000 calculates the stress amplitude from the amplitude of vibration, thereby permitting the determination of the stress load on the test specimen from the images. Thus, the HPV-X2 can effectively serve in the very important fatigue testing process during product development.