Metal and Alloy Materials Testing
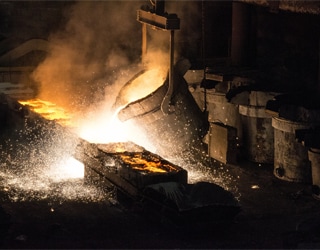
Testing, Analysis and Inspection of Metals and Alloys
Shimadzu manufactures a complete range of analytical tools for the evaluation of all types of metals from the traditional precious metals used in fine jewelry to modern ultra-lightweight alloys used in jet aircraft.
Below are some examples:
ASTM Method Applications
ASTM Method | Recommended Solution | |
---|---|---|
ASTM E8 | Standard Test Method for Tension Testing of Metallic Materials | AGX-V, AGS-X, Wedge Grips, Extensometers |
Featured Applications
Multifaceted Evaluation of EV Drive Motor Shaft Produced by Radial Forging
Radial forging is an innovative forging technology of hollow shaft which makes it possible to form the outer and inner diameters of parts at the same time by applying force from the radial direction of hollow shafts or hollow axis with a hammer (die) while simultaneously inserting a core bar into the shaft to transcribe the inner diameter shape. Hollow shafts produced by the radial forging process are attracting attention as next-generation shafts that satisfy both strength and weight reduction. In addition to the evaluation of the mechanical properties of motor shafts by the static tensile test and hardness test described in previous reports. In this Application News, an elemental analysis using an electron probe microanalyzer (EPMA) and evaluation of thermal properties with thermal analysis instruments were newly conducted. This article introduces an example of a multifaceted evaluation of motor shafts comparing the results of various types of measurements.
Evaluation of Electric Vehicle (EV) Motor Shafts Produced by Radial Forging: Radial Forging Processing Affects Static Tensile Characteristics
In forging processes such as radial forging, the product is formed to the target shape while also increasing its strength by refinement of the crystal grain structure by deformation of the metal surface by hammering (i.e., forging). For this reason, it is important to identify the region which is affected by the forging process, that is, how far the effect of forging extends from the surface layer into interior of the material. This article introduces an example in which samples were actually cut from a radial forging, and differences in their mechanical properties depending on the position were assessed from the surface layer to the interior.
Evaluation of Press Work on Sheet Metal
Pressed parts made of lightweight materials with poor workability, such as high tensile steel, aluminum alloys, and magnesium alloys, are essential for reducing the weight of transportation equipment. Repeatedly modifying the die to achieve a target shape not only increases costs, but also lengthens the development period. One solution currently being tried is to reduce the number of actual samples evaluated by using simulation to predict forming problems in advance. As simulation technology continues to evolve, the use of methods such as the Yoshida-Uemori Model, which considers a greater number of factors than previous methods, including plastic strain dependence of elasticity based on the r-value and the Bauschinger effect, has increased.
Tensile Test of Metallic Material by Strain Rate Control Using an Automatic Extensometer
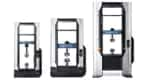
This article introduces an example in which the possibility of conducting ISO 6892-1:2019 compliant strain rate control was verified using a Shimadzu Autograph AGX™-100 kNV precision universal testing machine and an SIE-560SA automatic extensometer.
Tensile Test of High Tensile Strength Steel
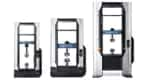
There is a deeply rooted need for tensile strength tests for extremely thin copper foil used for printed circuits and packaging materials in electronic and food industry. Practical tests, however, are often confronted with the problem of getting reliable data due to fluctuations and breakage of the specimen at the gripped portion. Consequently, static tensile tests of extremely thin foils as thin as 0.02mm must be conduced in a manner different from general tests. The following is an introduction of testing methods for highly reliable test results and some ideas on grip that encourage normal breakage of the specimen.
Static Tensile Test of Extremely Thin Copper Foil Selection of Optimal Grips and Grip Faces (I)
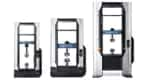
There is a deeply rooted need for tensile strength tests for extremely thin copper foil used for printed circuits and packaging materials in electronic and food industry. Practical tests, however, are often confronted with the problem of getting reliable data due to fluctuations and breakage of the specimen at the gripped portion. Consequently, static tensile tests of extremely thin foils as thin as 0.02mm must be conduced in a manner different from general tests. The following is an introduction of testing methods for highly reliable test results and some ideas on grip that encourage normal breakage of the specimen.
Static Tensile Test of Small Pipe Selection of Optimal Grips and Extensometers (II)
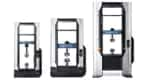
The mechanical properties of aluminum and copper pipes, often used in air conditioners and in various precision instruments, must be evaluated in the form of their actual use. Static tests are conducted with both ends of the pipe specimen processed flat and the center portion remaining in the form of a pipe, while conventional testing methods are performed by inserting a core into the gripped part of the specimen to prevent crushing. Actual test conditions and test results are introduced here.
Observations of Turbine Defects (X-ray CT)
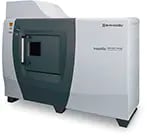
X-ray fluoroscopy systems offer non-destructive observations of the internal structures of objects. They are effective instruments for identifying the cause of failure of industrial products. By simplifying the non-destructive tomographic imaging and 3D imaging of the interior of objects, observations of internal shapes, dimensional measurements, and density observations, these systems provide a powerful tool for defect analysis and quality control.
Automatic Elongation and Width Measurements In Tensile Tests of Thin Steel Plates
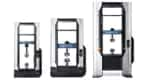
Simply attach an automatic extensometer and width sensor to the Autograph precision universal tester to automate the measurement of various physical properties, including r-values, which are useful in evaluating the workability of steel plates. This enables easily performing tests that conventionally used manual extensometers and width sensors, or strain gauges.
Evaluation of Functioning of Shape Memory Alloys in Automatic Stress-Strain Control Mode of Shimadzu Autograph
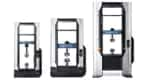
Shape memory alloys, drawing keen interest for their unique characteristics as metallic materials, are currently used widely in the fields of space exploration, the automobile industry, electronic instruments, medical instruments, and consumer goods. Further study to expand their application is going on. Change of shape, recovery ratio and recovery force are major factors of the shape memory effect. One area of inquiry of particular interest is how the change of stress and strain is influenced by temperature. The Shimadzu Autograph, an automatic stress-strain control device, can control loading rate and gauge length strain rate through its computer control system.
Evaluation of the Bauschinger Effect on a Steel Sheet Specimen Subjected to In-plane Reverse Loading Test
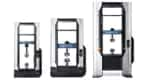
In dies manufacturing for presses, the spring-back phenomenon is an issue causing forming failures that need to be coped with by trial and error, which requires tremendous time and costs. In recent years, on the other hand, computer aided engineering (CAE) analytical technologies are utilized in various fields to simulate product designs on a computer for reducing the number of times and costs of trial production. Regarding dies manufacturing for presses, simulation is also coming to be used to predict the springback phenomenon in die design as an effective tool to achieve drastic cost reductions. This article presents an example of evaluating the Bauschinger effect on a 1 mm thick cold rolled steel sheet (SPCC) without buckling the sheet, using a Bauschinger effect measuring fixture.